Making chainplates
Making chainplates
Can anyone offer a reason not to fabricate your own chainplates? I am looking at replacing the 6 on my 25' boat, and I can get 304 stainless bar stock for a fraction of the cost of new chainplates. I don't mind the work in cutting and drilling, and I have access to tools capable of handling the material. Any reasons not to undertake this?
- Tim
- Shipwright Extraordinaire
- Posts: 5708
- Joined: Tue Apr 01, 2003 6:39 pm
- Boat Name: Glissando
- Boat Type: Pearson Triton
- Location: Whitefield, ME
- Contact:
Nope--by all means go for it.ryan wrote:Any reasons not to undertake this?
The drilling can be difficult, but with the right bits it's well within the realm. I made the chainplates for the daysailor, and wore out several 3/8" bits in the process. Otherwise, it was a cinch.
---------------------------------------------------
Forum Founder--No Longer Participating
Forum Founder--No Longer Participating
-
- Wood Whisperer
- Posts: 649
- Joined: Fri Aug 19, 2005 7:42 pm
- Location: South coast of Texas, Matagorda Bay
Made all the chain plates for my Trimaran. Also make the chain plates on the boats I build, when they require chainplates.
The tri used 1 1/2 by 1/4 stainless flat stock. I drilled all the holes using a drill press and cobalt bits. Keep them cool, don't spin them and you should be able to drill all the holes with one bit. For your clevises, go 1/64 oversize on the holes by the way, but no more. Then use a counterbore (or a very large bit) and break the edges of both sides of the holes. Not needed on those holes where the bolts go.
You WILL need a drill press.
The tri used 1 1/2 by 1/4 stainless flat stock. I drilled all the holes using a drill press and cobalt bits. Keep them cool, don't spin them and you should be able to drill all the holes with one bit. For your clevises, go 1/64 oversize on the holes by the way, but no more. Then use a counterbore (or a very large bit) and break the edges of both sides of the holes. Not needed on those holes where the bolts go.
You WILL need a drill press.
-
- Master of the Arcane
- Posts: 2272
- Joined: Sat Oct 04, 2003 10:55 pm
- Boat Name: Jenny
- Boat Type: 1966 Pearson Triton
- Location: Rowley, MA
- Contact:
Let the drill turn slowly, use some pressure and use lots of cutting oil when you drill those holes. With the right technique you shouldn't need to burn through drills. Did I just dis Tim? ... my apologies :-)
If the drill starts getting really hot then you need more oil/less pressure and speed. Once the drill gets to a certain temperature, the heat treatment is lost and the drill will basically melt down and the edge will be lost. The high heat will have also destroyed the heat treatment so there is no use re-sharpening the drill.
It will be a slow process.
Or you could buy a big pack of drills and just burn through them. It will cost more but it will be done much faster.
-Britton
P.S. I just read the other day that someone on the National Triton website made chainplates out of some sort of plastic. I don't think I would be up for that kind of experimentation considering the repercussions but to each their own.
If the drill starts getting really hot then you need more oil/less pressure and speed. Once the drill gets to a certain temperature, the heat treatment is lost and the drill will basically melt down and the edge will be lost. The high heat will have also destroyed the heat treatment so there is no use re-sharpening the drill.
It will be a slow process.
Or you could buy a big pack of drills and just burn through them. It will cost more but it will be done much faster.
-Britton
P.S. I just read the other day that someone on the National Triton website made chainplates out of some sort of plastic. I don't think I would be up for that kind of experimentation considering the repercussions but to each their own.
Ryan, I just recently dropped my old ones off at a machine shop and mine will be 316. My question is why are mine made with this angle piece.BTW they go thru deck then bolted to knees inside the hull. Colud I not just use a straight piece of stock bolted to the knee. Is there a reason it bends. The straight piece would then come out beam to beam ,but would have no bend ,but the clevis pin would make whatever bend?Or would that be to much of a lateral pull.
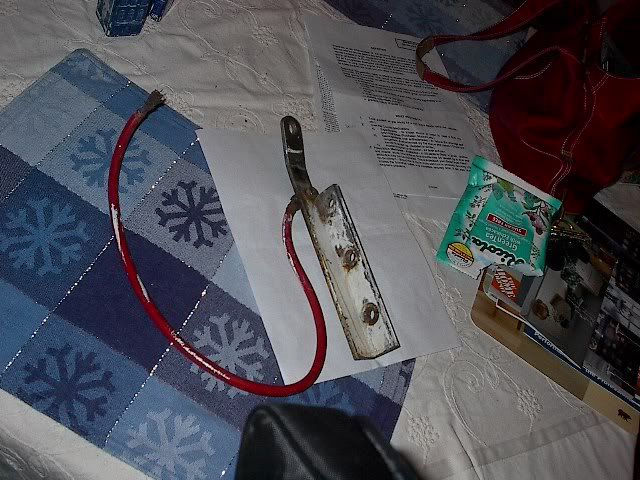
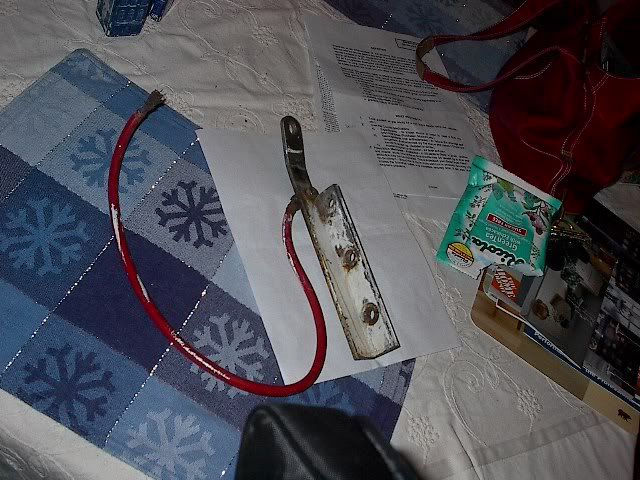
- Tim
- Shipwright Extraordinaire
- Posts: 5708
- Joined: Tue Apr 01, 2003 6:39 pm
- Boat Name: Glissando
- Boat Type: Pearson Triton
- Location: Whitefield, ME
- Contact:
Metalworking...it just ain't my bag, baby!bcooke wrote:Did I just dis Tim? ... my apologies :-)
My education never ends. Getting better at metalworking--and adding some requisite tools--is well up on my list.
---------------------------------------------------
Forum Founder--No Longer Participating
Forum Founder--No Longer Participating
stone
The old chainplates on my boat came through the deck the same way that yours do. I plan on turning my chainplates 90 degrees for two reasons. First, I can use a straight chainplate because the axis of the clevis pin will be parallel to the centerline on the boat and second, I can bolt the chainplate to the SIDE of my chainplate knees instead of behind them (the way it was originally) so they can be inspected. The only advantage I see to the bent chainplate is it saves some sidedeck room.
Thanks for all the tips guys!
Ryan
The old chainplates on my boat came through the deck the same way that yours do. I plan on turning my chainplates 90 degrees for two reasons. First, I can use a straight chainplate because the axis of the clevis pin will be parallel to the centerline on the boat and second, I can bolt the chainplate to the SIDE of my chainplate knees instead of behind them (the way it was originally) so they can be inspected. The only advantage I see to the bent chainplate is it saves some sidedeck room.
Thanks for all the tips guys!
Ryan
Ryan, yours are made with the L bracket piece of stock also? The bend in the last inch or so follows the direction of the rigging coming down. I think I am trying to do the same as you ,but am worried about having no bend where the turnbuckle hooks up to follow the angle of the rigging.Not sure what to tell machine shop guy yet? How are the chainplates on the Tritons?
-
- Wood Whisperer
- Posts: 649
- Joined: Fri Aug 19, 2005 7:42 pm
- Location: South coast of Texas, Matagorda Bay
When I re-rigged Tehani I installed toggles under EVERY turnbuckle. I suspect that bend is to help the chain plate line up with the shroud and turnbuckle to get a fair lead. I refuse to put turnbuckles on with out the toggles underneath for exactly that reason- then I KNOW they always lead fair. Of course I also moved the chain plates out to the side of the hull, rather than through the deck. Never again will I have deck leaks from chain plates *grin*
Britton- the other problem with over heating the work other than ruining the bit, is that it will work harden the stainless and then it'll be even harder to drill.
A slow speed, firm even pressure to keep it cutting and plenty of oil is the ticket.
Britton- the other problem with over heating the work other than ruining the bit, is that it will work harden the stainless and then it'll be even harder to drill.
A slow speed, firm even pressure to keep it cutting and plenty of oil is the ticket.
stone
Mine were not L-brackets, but using the L shape is a way for the manufacture to allow the chainplate to be bolted to the side of the chainplate knee while still having the chainplate exit the deck with the clevis hole axis perpendicular to the deck. This saves side deck space (though not very much), but my suspicions are exactly what Charlie said. It is cheaper to bend the chainplate to lead the shroud fair than it is to use toggles. That being said, I also agree with Charlie, and every one of my turnbuckles ends in a toggle.
Ryan
Mine were not L-brackets, but using the L shape is a way for the manufacture to allow the chainplate to be bolted to the side of the chainplate knee while still having the chainplate exit the deck with the clevis hole axis perpendicular to the deck. This saves side deck space (though not very much), but my suspicions are exactly what Charlie said. It is cheaper to bend the chainplate to lead the shroud fair than it is to use toggles. That being said, I also agree with Charlie, and every one of my turnbuckles ends in a toggle.
Ryan
-
- Master of the Arcane
- Posts: 2272
- Joined: Sat Oct 04, 2003 10:55 pm
- Boat Name: Jenny
- Boat Type: 1966 Pearson Triton
- Location: Rowley, MA
- Contact:
Interesting. I never thought of it but of course that makes sense.Britton- the other problem with over heating the work other than ruining the bit, is that it will work harden the stainless and then it'll be even harder to drill.
Better add another room opposite your new office for the metal working/ engine overhaul shop ;-) Better yet. Forget the whole idea and find a new best friend in the machinist trade.My education never ends. Getting better at metalworking--and adding some requisite tools--is well up on my list.
-Britton